Arbeitswelt radikal verändert
Es ist am 7. Oktober 1913 gewesen, als in der Ford-Autofabrik in Detroit auf eine völlig neue Produktionsweise umgestellt worden ist. Man begann mit dem Probebetrieb eines behelfsmäßigen ersten Montagebands für die Produktion des Modell T. Das Auto sollte eine einzigartige Erfolgsgeschichte schreiben, seine Produktionsweise die Welt revolutionieren.
Dieser Artikel ist älter als ein Jahr.
Unternehmer Henry Ford ließ über das Fließband Zündmagneten für das Modell T montieren, das er seit 1908 baute und das die Motorisierung der USA einleitete. Die Fertigungszeit der Magneten verkürzte sich auf dem Band von 20 auf fünf Minuten. Es folgte das Fahrgestell, das bisher in zwölf Arbeitsstunden gefertigt wurde. Es verließ nun bereits nach eineinhalb Stunden das in der Anfangsphase noch von einem Seil gezogene Fließband. Bald wurde auf diese rationelle Weise der ganze Wagen zusammengesetzt.
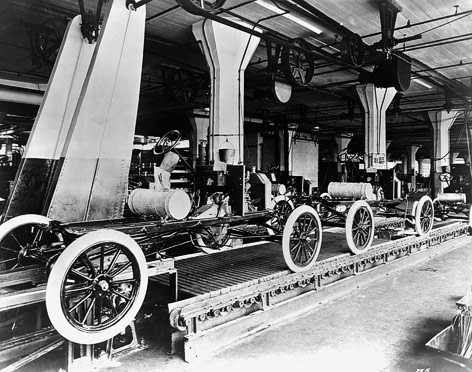
Corbis
Ein Mann, ein Handgriff lautet die Devise
Vorbild Fleischverarbeitung
Das Fließband hatte ein Vorbild: eine Fleischwarenfabrik in Chicago. Ford beobachtete, wie die Rinder- und Schweinehälften durch eine Kettenbahn von einem Arbeitsplatz zum anderen weitertransportiert wurden. Jeder Schlachter war auf bestimmte Handgriffe spezialisiert. Das Fleisch konnte viel schneller und fachgerechter verarbeitet werden. Aber erst die Übernahme dieses Produktionsprinzips in der Automobilindustrie und die vollständige Automatisierung dort machten das Fließband zum umstrittenen Symbol einer neuen Zeit.
Mehr und billiger
Ford selbst beschrieb den Grundgedanken als „Verminderung der Ansprüche an die Denktätigkeit des Arbeitenden und eine Reduzierung seiner Bewegungen auf das Mindestmaß“. Das - so die Idee - erhöhe die Produktivität und die Stückzahlen. Das Auto wurde dank der billigen Herstellung zu einem Massenprodukt - ganz in Sinne Fords, der auf Preissenkungen setzte, um seinen Absatz zu steigern. Extras gab es keine. Angeblich sagte Ford, der Kunde dürfe sich jede Farbe aussuchen - so lange sie schwarz sei.
Ford drückte den ursprünglichen Preis von 850 Dollar mit Hilfe des ersten Fließbandes und der Massenproduktion später auf 260 Dollar. Ford produzierte 1914 mit 13.000 Arbeitern 300.000 Autos, während 299 andere Autohersteller mit 66.350 Beschäftigten nur 280.000 Autos bauten.
Massenproduktion und Massenkonsum
Neben dem Fließband war es aber auch eine zweite Innovation, mit der Ford seinen Erfolg begründete. Ford verdoppelte 1914 die Löhne seiner Arbeiter auf fünf Dollar pro Tag gegenüber 2,34 Dollar und reduzierte gleichzeitig die tägliche Arbeitszeit von neun auf acht Stunden. Andere Unternehmen folgten dem Beispiel nach anfänglichem Widerstand.
Fords Vorstoß kam freilich nicht aus reiner Nächstenliebe: Drei Monatsgehälter waren etwa so viel wie der Preis eines Modell T. Es wurde also nicht nur das Produkt geschaffen, sondern quasi auch die Abnehmer. Auf die Massenproduktion folgte die Sicherung des Massenkonsums. Als Fordismus sollte dieses Prinzip in die Wirtschaftsgeschichte eingehen.
Die späte Krise des Fordismus
Jahrzehntelang regierte dieses System, ehe es in die Krise kam. Die Unzufriedenheit der Arbeiter mit dem eintönigen Alltag wuchs. Auch aus wirtschaftlicher Sicht kamen bald Zweifel auf: Unflexibel und störungsanfällig war die Produktion, ein Fehler legte gleich den gesamten Ablauf lahm. Hinzu kam die stetig zunehmende Automatisierung, Arbeiter wurden mehr und mehr durch Maschinen ersetzt. Die Industrie war auf dem Arbeitsmarkt ohnehin bereits gegenüber der Dienstleistungsbranche im Rückzug begriffen.
Ab den 1970er Jahren wurden die Produktionsweisen auch in der Autoindustrie dann zunehmend flexibler. Hersteller wie Toyota setzten auf die Gruppenfertigung statt auf starren Fließbandtakt. Dennoch ist die Arbeit am Fließband noch heute tägliche Realität für Millionen Menschen - nicht nur in der Fertigung von Produkten in Schwellenländern für den westlichen Markt.
Links: